Staying competitive in today's rapidly changing manufacturing environment and rapid development demands more than cutting-edge technologies or efficient processes.
To improve operational efficiency in manufacturing, process engineers and data scientists need a comprehensive strategy to maximize output, foster cooperation, and boost effectiveness.
Traditional machine learning (ML) systems often fail to address these professionals’ specific problems because they can’t provide real-time insights and bridge the gap between process engineering and data science.
Hybrid modeling represents the intersection between traditional ML and the first principal engineering differential equations. By leveraging data in combination with engineering knowledge, modeling reliability can be highly improved for even biased and noisy industrial environments.
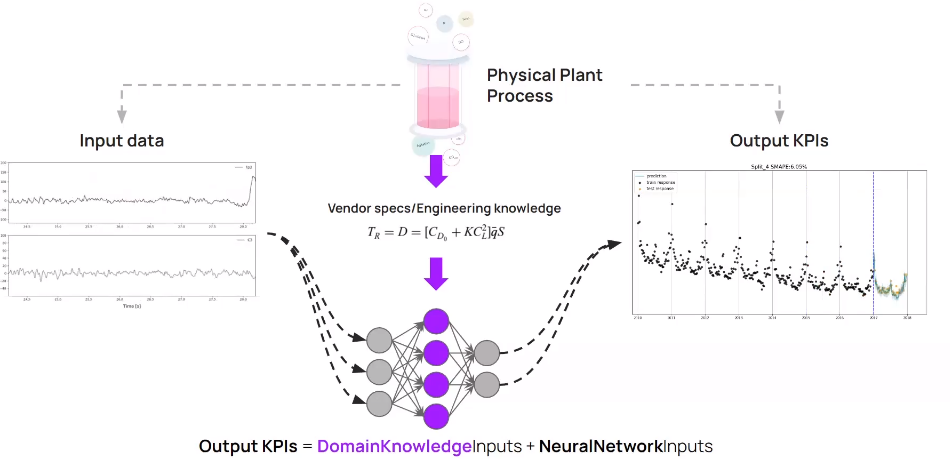
In this article, we will discuss operational efficiency in manufacturing and provide you with strategies, examples, and use cases that will help you improve your processes.
Finally, we will introduce Basetwo – a process optimization software that uses the power of physics-informed/hybrid machine learning to deliver unparalleled insights, revolutionizing how industry professionals gain valuable knowledge in real time.
What is operational efficiency in manufacturing?
Operational efficiency refers to the capability of an organization to utilize its resources effectively to produce goods or deliver services with optimal productivity, quality, and cost-effectiveness.
Operational efficiency focuses on improving efficiency in various facets of a company's operations, such as:
- Production and manufacturing processes
- Supply chain management
- Inventory control
- Resource utilization
- Employee training
- Workflow management.
The goal is to streamline operations, reduce waste, eliminate unnecessary steps or redundancies, increase production, and optimize the utilization of resources such as labor, materials, and equipment.
Doing so aims to maximize output and minimize cost – to achieve operational efficiency at its peak. A company's operational efficiency is typically measured by key performance indicators (KPI), some of which are:
1. Overall equipment effectiveness (OEE)
OEE is a crucial statistic for operational and manufacturing efficiency that assesses machinery and equipment performance, availability, and quality. It offers insights into the efficacy and efficiency of various production lines and operations. OEE is calculated by the formula below:
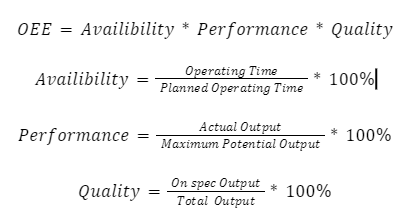
In typical manufacturing industries, OEE is benchmarked at 80-90%, and the reason for this is that for any manufacturer to achieve 100%, OEE would require complete utilization of resources, which is directly related to inventory. The graph below illustrates how a high utilization rate will result in an infinite inventory
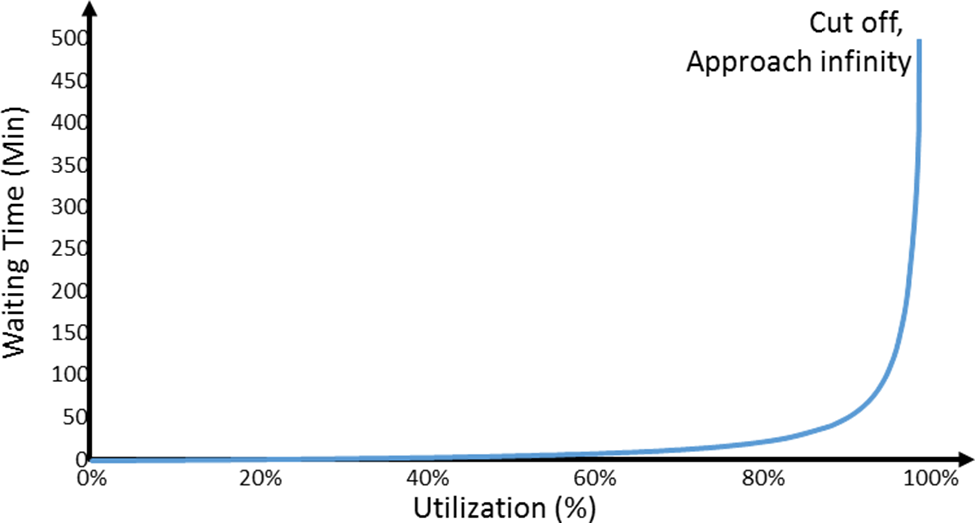
2. Reducing cycle time
It represents the time it takes to complete a specific process or operation from start to finish. Monitoring cycle time increases productivity and helps identify bottlenecks, production delays, and inefficiencies within the production workflow.
You can calculate it with this formula:

A benchmark cycle time varies for each industry depending on the products being produced and is usually targeted based on historical data.
3. Reducing downtime
Downtime measures the time equipment, machinery, or processes are not operational due to maintenance, breakdowns, changeovers, or other factors.
Minimizing downtime is a critical metric in further improving manufacturing and operational efficiency, as it directly correlates with equipment availability.
4. Energy and resource consumption
Monitoring energy consumption and resources, such as electricity, water, or raw materials, provides insights into efficiency improvements and sustainability efforts and ensures cost-effective resource utilization.
5. Production yield
The production yield measures the percentage of defect-free products or outputs produced to the total number of units of the same output manufactured using the same input. A higher production yield indicates efficient processes, quality control, and more output.
For most manufacturing companies, the overall yield is between 95-100 same or more revenue-%, with first-pass yields typically between 85-95 %.
6. Inventory turnover
A key indicator gauges how rapidly a business sells or uses up its stock over a specific period and saves time. It is derived by dividing the average inventory value by the cost of goods sold (COGS).
An increased inventory turnover ratio shows that excess inventory is used effectively, lowering holding costs and offering effective inventory management.
An inventory ratio between 4 and 6 indicates a good balance between sales and restocking.
7. Stockout rate
Stockouts occur when a company runs out of stock and can’t meet customer demand. Monitoring the stockout rate helps identify insufficiency in inventory management and enables organizations to take corrective actions.
How to improve operational efficiency in manufacturing
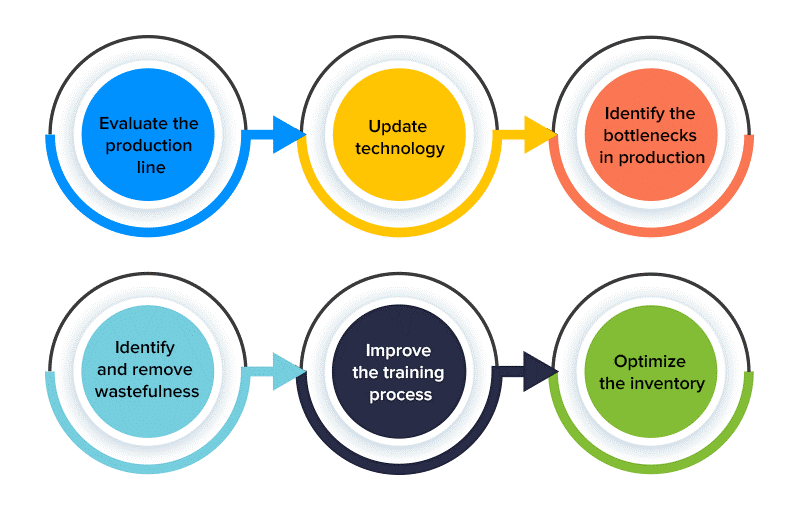
Businesses interested in improving operational efficiency know its impact on sales, profits, and customer happiness.
According to the Annual Global CEO poll, 72% of 1,400 global CEOs prioritize and depend on operational efficiency to enhance their revenues. Here are some key strategies to improve operational efficiency in your manufacturing operations:
1. Utilize technology
Research indicates that utilizing technology and digitalization has vastly improved worker productivity for the employees of businesses worldwide by 52%. Business management performance increased by 49%, while there was also an increase in meeting customer expectations by 46%.
By leveraging advanced process optimization and control software such as Basetwo, manufacturers can build, test, and operationalize models that simulate real-life processes.
Engineers and data scientists can analyze various scenarios, identify inefficiencies, and implement improvements.
Basetwo provides a platform specifically designed for the manufacturing industry and empowers process engineers and data scientists to harness the speed, scalability, and accuracy of machine learning while understanding the underlying dynamics of their processes.
2. Create robust & reproducible SOPs
Standard Operating Procedures (SOPs) ensure consistency and efficiency in any manufacturing process. A good SOP outlines the steps, redundant processes, guidelines, and best practices required to perform a specific task or operation.
It should be comprehensive, easily understandable, and regularly updated to reflect process improvements or changes. A well-crafted SOP minimizes errors, reduces variability, and enables employees to execute tasks precisely, optimizing operational efficiency.
>>Download our SOP free template here<<
3. Enable cross-functional collaboration
Collaboration among different departments and stakeholders within a manufacturing organization is essential for improving operational efficiency. Lack of collaboration can harm a business organization's operations and cause the following:
- Duplication of work, leading to waste of time, resources, and energy.
- Misalignment of goals results in disjointed efforts that reduce overall operational efficiency.
- Communication breakdowns cause misunderstanding, delay, and errors that interfere with making real-time decisions.
- The restriction of knowledge and expertise to specific individuals and teams impedes sustainable operations, problem-solving, and the implementation of best practices.
The most challenging hurdle is fostering collaboration between engineering and data science because these fields have different specialties and viewpoints on the same issues. AI technology for process optimization can aid with this time-intensive endeavor.
Basetwo provides a platform that facilitates better collaboration by providing a shared environment where process engineers, process modeling experts, and data scientists can work together seamlessly.
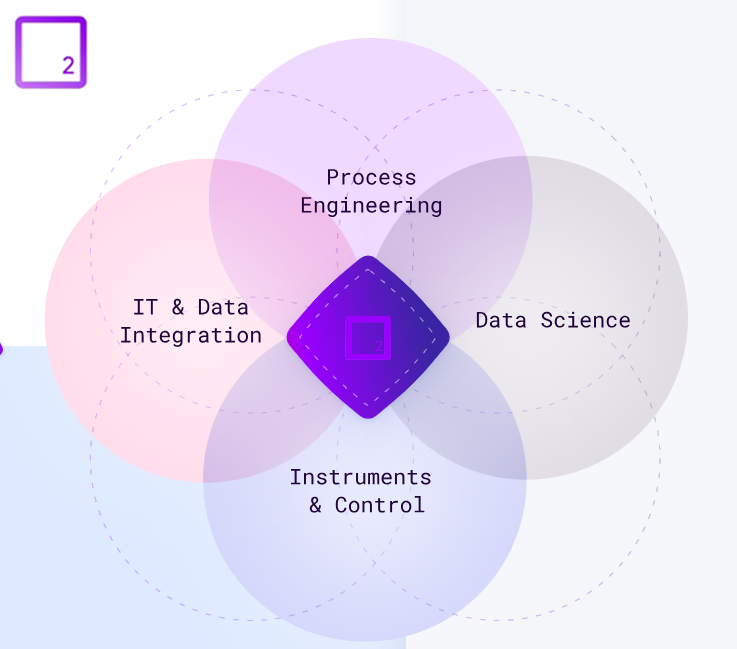
4. Monitor performance and KPIs
Continuous monitoring of performance and KPIs is critical for measuring progress and identifying areas for improvement. Manufacturers should establish a set of relevant KPIs that align with their operational goals and regularly track and analyze them.
KPIs such as cycle time, production yield, equipment uptime, and resource utilization production and consumption provide insights into process efficiency and help identify bottlenecks or areas of waste.
Basetwo offers real-time data monitoring capabilities with its digital twin life cycle technology, allowing manufacturers to gain visibility into their operations and make data-driven decisions for continuous improvement.
Examples of improved operational efficiency in manufacturing
Basetwo improves operational and manufacturing efficiency by providing AI models for process engineering, reducing cycle time and yield, reducing downtime, and optimizing production. It also offers predictive maintenance, dynamic process optimization and control, and independent inspections for product compliance with specifications and codes.
Let us look at the following examples to understand further how Basetwo can enable customers and manufacturers to increase operational efficiency and stream business operations.
- Real-time optimization of solvent Swap distillation column to reduce cycle time by accurately predicting product purity parameters.
- Optimizing heat exchanger performance by accurately predicting and recommending heat exchanger maintenance, thus reducing the effects of fouling and frequent cost of cleaning.
- Optimizing flight time by predicting possible failure components in heavy fuel engines enables engineers to identify and prevent operational failures proactively. It uses fault detection models for individual engine components with the help of deconstructed models.
- Real-time process optimization in refineries using hybrid advanced process control systems and surrogate models that use live plant data to make real-time decisions. It increases process performance and improves environmental compliance and plant safety while increasing plant reliability.
Up to this point, we have assisted Fortune 500 firms in cutting cycle time and operational expenses by over 40% and energy use and scope 1/2 emissions by 25%.
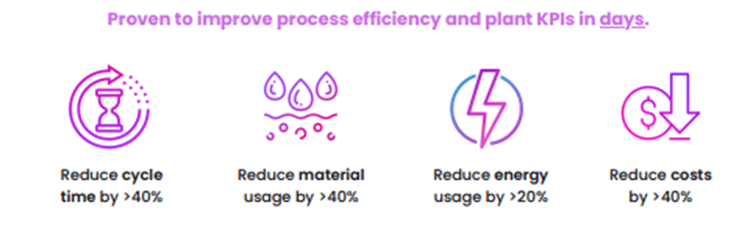
See how Basetwo can further improve the efficiency of the operating expenses and margins for customers in detail:
Case study: Real-time optimization of solvent swap distillation columns
Solvent swap distillation separates and purifies chemical mixtures based on their volatilities using different solvents to extract specific components through distillation.
Problem scenario
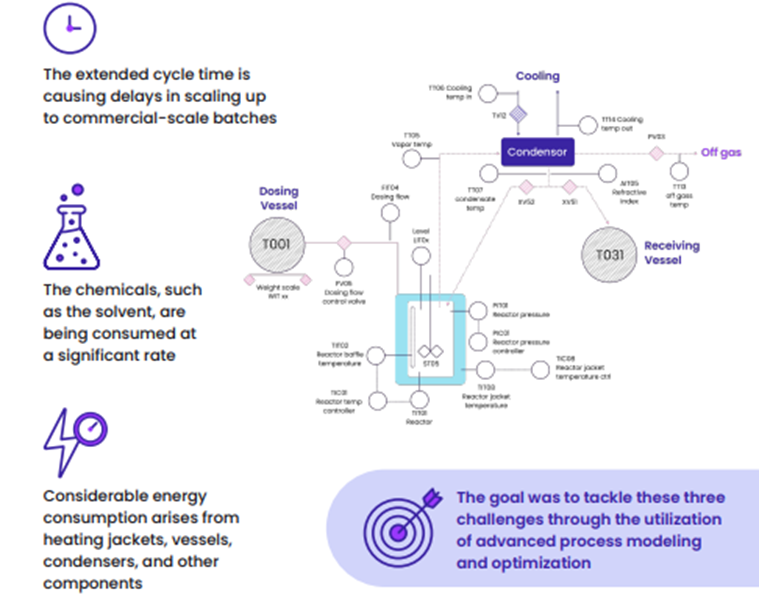
Basetwo customers trusted us to optimize the pilot plant to be scaled up to commercial scale batches and solve the following challenges:
- Reduce cycle time that was longer than twenty hours
- Reduce chemical/solvent consumptions to minimize operating costs
- Optimize energy consumption of the plant to minimize operating costs
Basetwo objective
The objective of Basetwo was to address these three challenges using the latest technology, advanced process modeling, and optimization through its hybrid model technologies.
Basetwo solution methodology
A first principal model of the existing technology was built, and real-time plant data was collected. By using a sequential modeling approach, a hybrid model was constructed.
The combined features of the first principal model and machine learning to minimize the error between simulated results and real-time plant performance is graphically illustrated below:
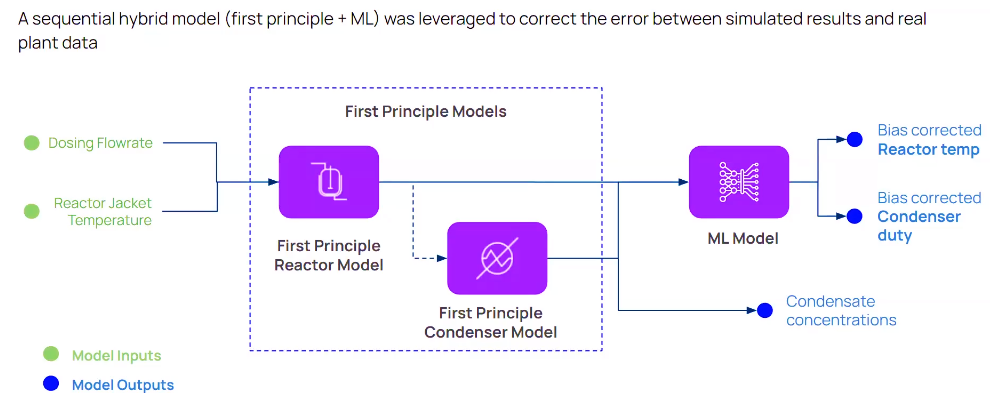

Impact of adding machine learning
On adding the machine learning corrections to the simulation results variance between live plant parameters and the simulated result was significantly decreased, as illustrated below:
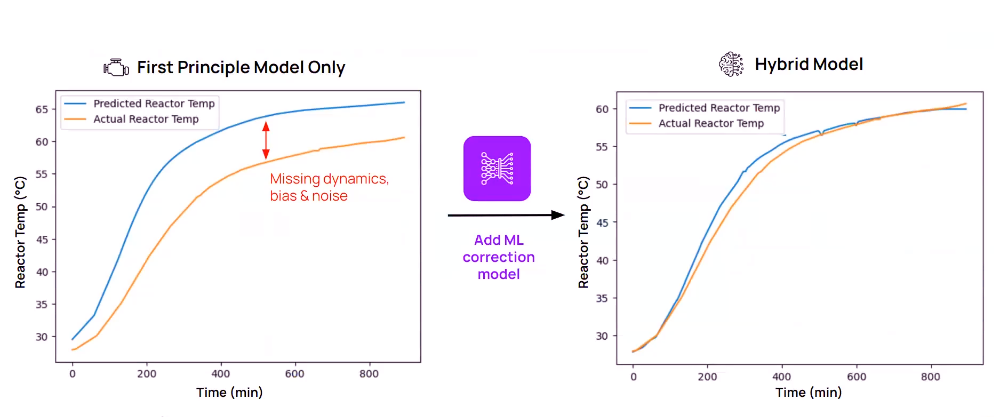
Basetwo proposed strategies
The Basetwo team suggested the following approach:
- Predictive stoppage of the batch using software sensing to measure purity without changing and standard operating procedure (SOP)
- Implementing an AI-modified SOP within ±30% marring of the current SOP.
- Implementing a completely AI-generated SOP within the constraints of design limitations.
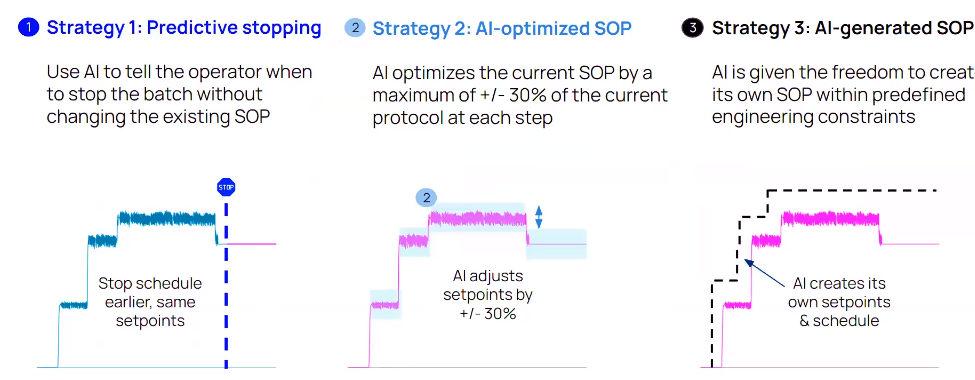
Results and benefits
On implementing the above process, the following benefits for customer acquisition were predicted, and customers were allowed flexibility to choose a solution that is best suitable to meet the demand and their needs.
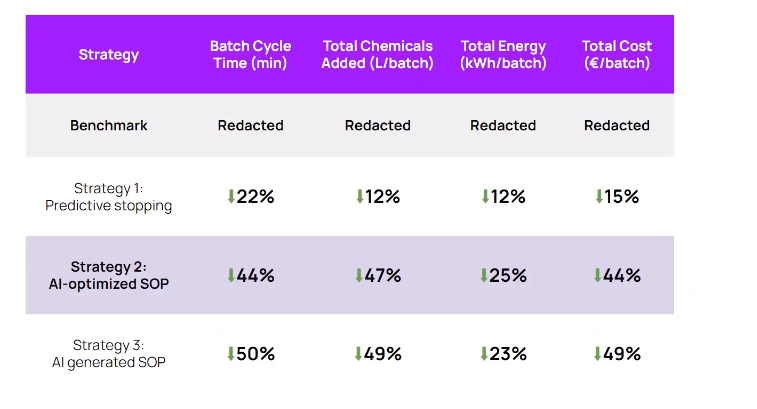

Conclusion
Basetwo hybrid model technologies offer flexible solutions for operational efficiency, boosting employee productivity and competitiveness with its creative approach and commitment to client success.
With Basetwo, businesses can confidently optimize their operations and keep up with the changing oil and gas industry. Choose Basetwo to gain unparalleled accuracy and priceless insights.
Contact us today for a demo and increase your business's operational and manufacturing efficiency.
FAQs
1. How do you measure operational efficiency in manufacturing?
Operational efficiency an be measured by monitoring Key performance indicators (KPI); some of the metrics that enable us to measure and improve operational efficiency are:
- Overall equipment effectiveness
- Cycle times
- Waste reduction
- Energy and resource management
- Inventory control and management
- Production yields
- Product quality and compliance
2. What are ways to create operational efficiency?
The following four steps to create operational efficiency are:
- Identify critical information and define key processes within the organization's workflow.
- Analyze and streamline the identified processes.
- Set performance metrics and targets for monitoring operational efficiency.
- Implementing a continuous improvement and feedback system to create operational efficiency is ongoing.
3. Is operational efficiency the same as production efficiency?
The terms operational efficiency ratio and production efficiency are not interchangeable, although they both fall under the umbrella of total company efficiency. Operational efficiency involves an organization's ability to efficiently use resources, achieve desired outcomes, reduce costs, manage resources, and minimize waste. Production efficiency measures a manufacturing process's effectiveness and operating efficiency, evaluating the use of labor, machinery, materials, and resources for product or service production.