Cement manufacturing is a critical industry, playing a central role in the development of infrastructure worldwide. However, it is considered a "hard-to-abate" industry1, meaning it’s difficult to lower greenhouse gas emissions and necessitates innovative solutions to create more sustainable processes.
With advancements in artificial intelligence (AI), the cement manufacturing process can achieve transformative improvements, addressing environmental, energy, and quality control issues.
.png)
Main Challenges with Cement Manufacturing
Reducing Environmental Impact and Regulatory Compliance
Cement production is a highly carbon-intensive industry, responsible for approximately 7% of global CO2 emissions.2 The dry kiln process involves using high temperatures to convert raw materials, mainly limestone and clay, into clinker, the main component in cement. About 60% of these emissions result from the chemical transformation during heating, while the remaining 40% stem from the fuel used to heat the kilns.3
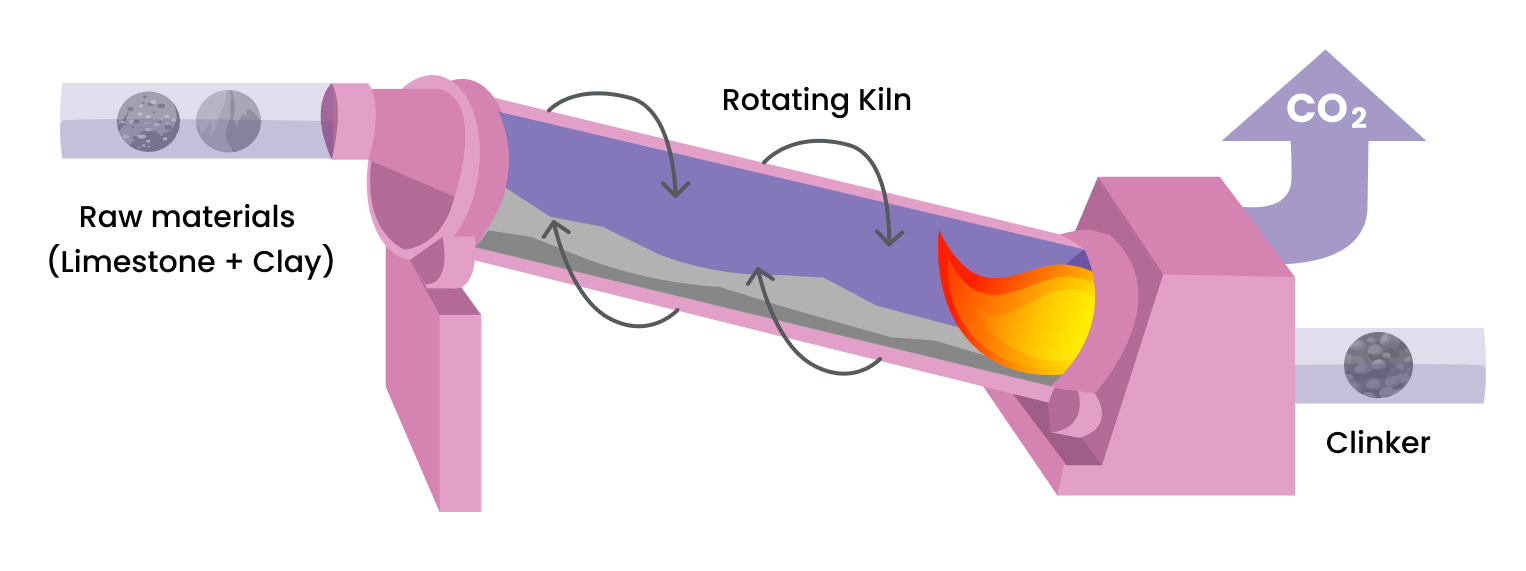
As urbanization accelerates, the demand for cement, a key ingredient in concrete, continues to rise. This growing demand exacerbates environmental concerns and complicates efforts to reduce emissions.
Cement manufacturers face increasing pressure to comply with regulatory requirements, such as air quality standards, emissions limits, and waste management regulations, all while striving to minimize their carbon footprint.
Improving Energy Efficiency within Cement Manufacturing
The cement production process demands intense heat, reaching up to 1450°C, to convert limestone into clinker, as illustrated in Figure 2. This high energy requirement positions cement production as one of the most energy-consuming industries globally.
It is estimated that the cement industry consumes about 5% of total global industrial energy4, with nearly 70% of energy in a cement plant being used in the grinding process – the crushing and grinding of raw materials and clinker.5
Finding ways to enhance energy efficiency is crucial for reducing operational costs and environmental impact.
Variability in Cement Quality & Fine Particle Size
Consistency in product quality is a significant concern in cement manufacturing. Variability can arise from fluctuations in raw material properties and differences in production processes, making it difficult to maintain consistent fineness.
The crushing and grinding process contains multivariable characteristics and a high degree of load disturbances, complicating consistent control. Achieving uniform product quality and optimal particle size with minimal deviations in fine variability poses a challenge for cement manufacturers, particularly as they strive to optimize production processes for cost savings and decarbonization.
Cost of Production
The two major costs of cement production are fuel and raw materials, which account for approximately 20-30% and 30-40% of production costs, respectively.6
The cost of raw materials, such as limestone, is around $40 per ton of cement, while the cost of heat sources, like coal and petcoke, is about $20 per ton.7
Innovative approaches to reducing these costs, such as optimizing raw material utilization and streamlining production processes, are essential for cement manufacturers to improve their profitability.
AI Applications in Cement Manufacturing
AI-enabled Process Optimization for Reducing Environmental Impact
AI offers powerful tools for optimizing the cement manufacturing process, contributing to sustainability efforts.
AI-driven process optimization platforms, like Basetwo, can provide recommendations to optimize kiln operations, reducing the amount of CO2 generated in the cement production process. With real-time insights and predictive alerts, AI systems ensure emissions remain within regulatory limits, supporting cement plants in achieving sustainability goals without requiring substantial additional investments.
By analyzing plant data and simulating existing processes, AI models can enhance the efficient utilization of raw materials by analyzing production data to recommend the optimal mix and proportions. This minimizes the raw material needed while also maintaining consistent production quality.
These optimization methods can significantly reduce the environmental impact of cement production.
Energy Management & Efficiency in Cement Plants
AI algorithms can streamline production processes and reduce energy consumption by optimizing fuel usage and process parameters, helping cement plants operate more efficiently.
For example, manufacturers can optimize kiln operations using AI technologies. By leveraging digital twins—a virtual simulation of the physical production process—to perform what-if analysis, cement manufacturers can adjust parameters like temperatures and pressures to improve thermal efficiency and reduce fuel consumption.
Optimizing various process parameters and set points enables manufacturers to operate their assets and overall production more efficiently, leading to reduced energy consumption and overall process costs.
Quality Control for Cement Production
AI-driven automated inspection systems ensure product consistency by detecting and rectifying defects in real-time. Machine learning (ML) models can predict potential quality issues, allowing manufacturers to make adjustments before defects occur. This leads to higher quality products and reduces waste.
Additionally, AI modeling can support the optimization of cement formulations. Manufacturers are able to experiment with different components and portions, to determine which blends allow them to achieve their desired product quality and characteristics.
AI-enabled process optimization can help manufacturers determine optimal blending setpoints for new or existing formulations, resulting in reduced energy consumption, lower costs, and shorter production times, all while maintaining desired quality attributes.
Real-World Examples of AI in Cement Plants
Several companies have successfully integrated AI into their cement manufacturing processes, achieving significant efficiency gains and environmental benefits.
In a study by McKinsey, AI was used in an autonomous mode, continuously learning and adapting to changing conditions to maintain optimal performance. This approach minimized the need for human intervention and ensured peak efficiency, resulting in throughput and energy efficiency improvement rates of up to 10% for the cement plant.
Another example is Basetwo, whose AI copilot offers manufacturers AI modeling and data-driven recommendations to optimize existing processes while considering plant constraints. This approach has led to a reduction in energy consumption by up to 20% and production costs by up to 40% for some of their customers.
These examples demonstrate the potential of AI to enhance efficiency and sustainability in the cement industry.
Challenges and Considerations
Technical Expertise
Implementing AI systems in cement manufacturing requires skilled personnel who can manage and maintain these technologies. There is a growing need for professionals with expertise in AI and machine learning to support the industry's transition to smarter manufacturing processes.
Integration with Existing Systems
Integrating AI into cement plants often faces challenges such as compatibility with legacy systems and access to relevant data sets. Data can frequently be disparate, difficult to access, or not in a clean, usable state. Overcoming these integration hurdles is essential for the successful adoption of AI technologies.
Tools, like Basetwo, can be used to bridge these gaps, ensuring seamless integration and analysis of various data sources while offering a low-code, user-friendly environment to enable manufacturers without technical expertise to leverage AI effectively.
The Future of AI in Cement Manufacturing
AI Formulation Discovery
AI can assist in discovering more sustainable cement formulations, reducing reliance on traditional raw materials and lowering carbon emissions.
For example, clinker is responsible for approximately 90% of the emissions released in the cement manufacturing process,8 to further decarbonization initiatives, manufacturers can focus on reducing the amount of clinker in their formulations.9
AI can support manufacturers in this endeavor by allowing them to virtually experiment with various replacements, such as fly ash or blast furnace slag, and predict the final quality attributes of the cement mix. They can continue to simulate and optimize their formulation until it achieves their targetted quality while ensuring the lowest possible production cost and energy consumption.
This innovation could lead to the development of greener cement products that meet stringent environmental standards.
Smart Factories – Fully Automated Cement Plants
Smart factories, or fully automated and AI-driven cement plants, are becoming increasingly feasible. In these environments, there are various levels of human intervention, from partially automated while considering operator constraints to fully autonomous and entirely run with AI.
Semi-autonomous cement plants can provide cement manufacturers with directions and recommendations on how to best run their current operations, minimizing the need for physical testing of production processes and changes to blends, while reducing deviations within their real-time processes.
On the other hand, fully autonomous manufacturing, or “lights-out factories”, are environments without any human intervention. Connecting these smart factories to an AI-enabled real-time optimizer (RTO) elevates their capability, enabling fully autonomous operations while continuously enhancing optimization outcomes without human involvement.10
These environments support manufacturers in various aspects of production for maximum efficiency and sustainability.
Generative AI in Cement Manufacturing
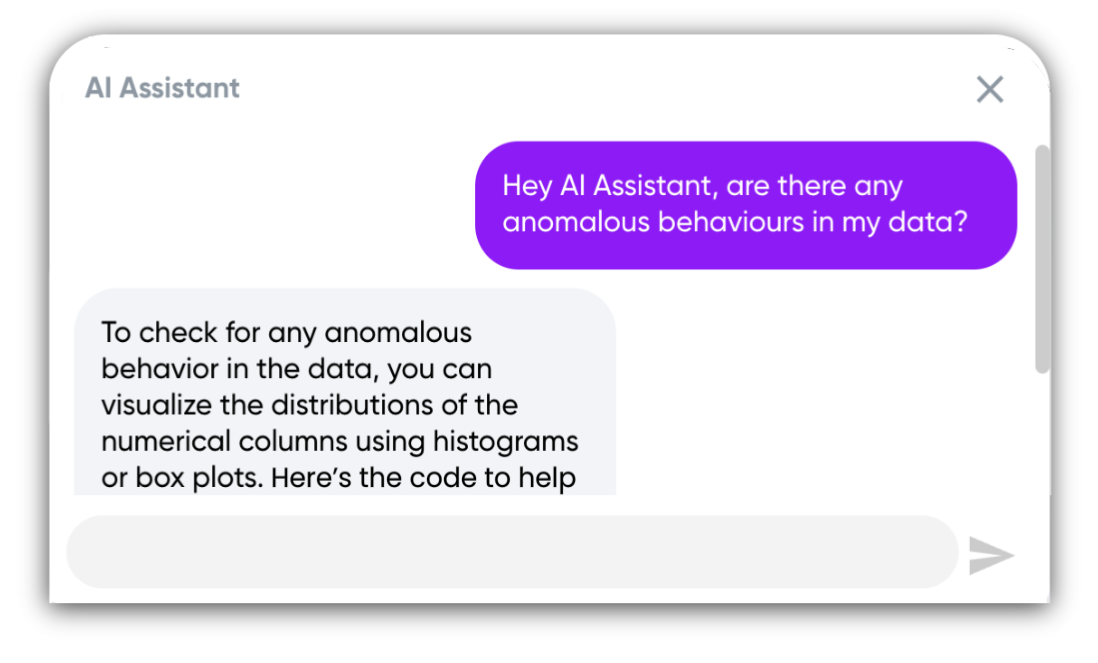
Generative AI is poised to revolutionize the cement industry by enabling manufacturers, even those without coding experience, to easily integrate various data sources, simulate, and optimize their production processes. Manufacturers can input plain language queries into generative AI models and receive the corresponding code as output.
One significant application of generative AI is in quality control. By analyzing plant data, manufacturers can identify deviations in product quality. Leveraging this technology with model-based optimization allows manufacturers to predict and maintain quality standards throughout the entire cement manufacturing process.
This democratization of AI technology makes it easier for manufacturers to achieve targets such as energy and cost savings, ultimately enhancing overall efficiency and sustainability.
Conclusion
The integration of AI in cement manufacturing is driving significant improvements in efficiency, quality, and sustainability. As the industry continues to face environmental and regulatory challenges, AI offers promising solutions to optimize processes, reduce energy consumption, and enhance product quality.
The future of cement manufacturing lies in the widespread adoption of AI technologies, paving the way for smarter, more sustainable production methods. By embracing these advancements, the cement industry can meet the growing demands of urbanization while minimizing its environmental impact.
For a tailored approach to decarbonization within your cement production, reach out to Basetwo today!
References:
- Chevron Policy, G. and P. A. (2024, May 3). Explainer: What do we mean by hard-to-abate industries?. chevron.com. https://www.chevron.com/newsroom/2024/q2/explainer-what-do-we-mean-by-hard-to-abate-industries#:~:text=The%20production%20processes%20for%20hard,produce%20more%20while%20emitting%20less
- Why is the cement industry labelled hard-to-abate?. DNV. (n.d.). https://www.dnv.com/article/why-is-the-cement-industry-labelled-hard-to-abate--241192/
- Brad Griffin – March 16, 2023. (2023, October 20). Concrete ways to reduce emissions from the cement sector. 440 Megatonnes: Tracking Canada’s path to net zero. https://440megatonnes.ca/insight/concrete-ways-to-reduce-emissions-from-the-cement-sector/
- Soomro, M., Tam, V. W. Y., & Jorge Evangelista, A. C. (2023). Production of cement and its environmental impact. Recycled Concrete, 11–46. https://doi.org/10.1016/b978-0-323-85210-4.00010-2
- de Goes Arantes, J. (2021, April). Process Optimisation Solutions. Rockwell Automation. https://literature.rockwellautomation.com/idc/groups/literature/documents/ar/cement-ar001_-en-p.pdf
- Pabon, A. (2014, August 18). Must-know: The cost elements of Cement. Market Realist. https://marketrealist.com/2014/08/must-know-cost-elements-cement/
- Cement costs and Energy Economics. Thunder Said Energy. (2023, June 21). https://thundersaidenergy.com/downloads/cement-costs-and-energy-economics/#:~:text=The%20breakdown%20of%20costs%2C%20in,ton%20for%20electricity%3B%20and%20%2420%2F
- Feldmann, R. (2019, December 31). Artificial intelligence helps cut emissions and costs in cement plants. McKinsey & Company. https://www.mckinsey.com/industries/chemicals/our-insights/artificial-intelligence-helps-cut-emissions-and-costs-in-cement-plants
- Heincke, S., Maksimainen, J., & Reiter, S. (2023b, February 3). Decarbonizing cement and concrete value chains: Takeaways from Davos. McKinsey & Company. https://www.mckinsey.com/industries/engineering-construction-and-building-materials/our-insights/decarbonizing-cement-and-concrete-value-chains-takeaways-from-davos
- Brad Griffin – March 16, 2023. (2023a, October 20). Concrete ways to reduce emissions from the cement sector. 440 Megatonnes: Tracking Canada’s path to net zero. https://440megatonnes.ca/insight/concrete-ways-to-reduce-emissions-from-the-cement-sector/